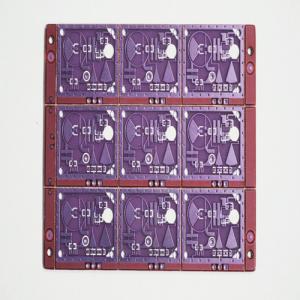
Add to Cart
5.8GHZ / 24GHZ Antenna Sensor Module High Frequency PCB Circuit Boards
Sensor PCB boards Specification:
Number of layer: 2
Board size: 2.2*2.2cm
Panel size: 30*18cm
Color: Green solder mask black silk screen
Craft edge:yes
Surface finish: Immersion gold
Material: Rogers 4350 0.254mm
Gerber file: required
Name:24GHZ Rogers K-band X-band Rigid Custom PCB Boards for Automatic Door Module
Automatic Door / Sensor Lamp Rigid PCB 2 Layer Control Board With Rogers Material Raw
Sensor PCB information:
The current civilian Doppler microwave sensors are operating in C-band (5.8GHz), X-band (10.525 / 10.687GHz) and K-band (24.125GHz), its transmit power less than 10 mW, are specified in the ITU You do not need to apply for the use of the frequency ISM band. Detection pattern omnidirectional and directional, depending on the antenna gain and transmit power, the detection range of 0.1 to 50 meters.
Microwaves emitted by the transmitting antenna, will be absorbed or reflected by the object is encountered, the power change. If the receiving antenna through the use of the object from the measured object or microwave reflected, and converts it into an electrical signal, and then processed by the measurement circuit, to achieve a microwave detection. Microwave sensors mainly by the microwave oscillator and the microwave antenna. Microwave oscillator is a device for generating microwaves. There are microwave oscillator device comprising klystron, magnetron or some solid elements. An oscillation signal generated by the microwave oscillator required waveguide transmission, and through the antenna out. In order to launch a consistent directional microwave antenna should have a special structure and shape.
PCB Sensor Specifics
At a high level, the capacitive sensor dependencies can be visualized by understanding the basics of a plate capacitor.
First the base capacitance must be accounted for. The term “base capacitance” refers to the measurement result of an “untouched” or uninfluenced sensor element. For simplicity, the base capacitor can be assumed to be constructed from the sensor pad on the topside of the PCB and the ground pour on the bottom side of the PCB.
The PCB itself makes up the “d” in the equation. As mentioned earlier, as d gets smaller (such is the case with flex PCBs), the baseline capacitance increases resulting in reduced sensitivity. The permittivity of free space (ε0) and the material (εr ) define the dielectric constant of the PCB insulator and will affect the ultimate base value. The area of the sensor, “A”, is typically limited to the size of the interacting finger.
High frequency PCB range:
Frequency Range: High-frequency PCBs are designed to operate in frequency ranges typically starting from a few megahertz (MHz) and extending into the gigahertz (GHz) and terahertz (THz) ranges. These PCBs are commonly used in applications such as wireless communication systems (e.g., cellular networks, Wi-Fi, Bluetooth), radar systems, satellite communication, and high-speed data transmission.
Signal Loss and Dispersion: At high frequencies, signal loss and dispersion become significant concerns. High-frequency PCBs employ techniques to minimize these effects, such as using low-loss dielectric materials, controlled impedance routing, and minimizing the length and number of vias.
PCB Stackup: The stackup configuration of a high-frequency PCB is carefully designed to address signal integrity requirements. It typically consists of multiple layers of copper traces, dielectric materials, and ground planes. The arrangement of these layers is optimized to control impedance, minimize crosstalk, and provide shielding.
RF Connectors: High-frequency PCBs often incorporate specialized RF connectors to ensure proper signal transmission and minimize losses. These connectors are designed to maintain consistent impedance and minimize reflections.
Electromagnetic Compatibility (EMC): High-frequency PCBs must comply with electromagnetic compatibility standards to prevent interference with other electronic devices and to avoid susceptibility to external interference. Proper grounding, shielding, and filtering techniques are employed to address EMC requirements.
Simulation and Analysis: Designing high-frequency PCBs often involves simulation and analysis using specialized software tools. These tools allow designers to assess signal integrity, impedance matching, and electromagnetic behavior before fabrication, helping to optimize the PCB design for high-frequency performance.
Fabrication Challenges: Fabricating high-frequency PCBs can be more challenging compared to standard PCBs. The use of specialized materials, controlled impedance requirements, and tight tolerances require advanced fabrication techniques such as accurate etching, controlled dielectric thickness, and precise drilling and plating processes.
Testing and Validation: High-frequency PCBs undergo rigorous testing and validation to ensure their performance meets the desired specifications. This includes impedance testing, signal integrity analysis, insertion loss measurement, and other RF and microwave tests.
It's important to note that the design and manufacturing of high-frequency PCBs are specialized areas requiring expertise in RF and microwave engineering, PCB layout, and fabrication processes. Working with experienced professionals and consulting relevant design guidelines and standards is crucial to ensure reliable performance at high frequencies.
High frequency PCB description:
High frequency PCB material in stock:
Brand | Model | Thickness(mm) | DK(ER) |
Rogers | RO4003C | 0.203mm,0.305mm,0.406mm,0.508mm,0.813mm,1.524mm | 3.38 ± 0.05 |
RO4350B | 0.101mm,0.168mm,0.254mm,0.338mm,0.422mm,0.508mm,0.762mm,1.524mm | 3.48 ± 0.05 | |
RO4360G2 | 0.203mm,0.305mm,0.406mm,0.508mm,0.610mm,0.813mm,1.524mm | 6.15 ± 0.15 | |
RO4835 | 0.168mm,0.254mm,0.338mm,0.422mm,0.508mm,0.591mm, 0.676mm,0.762mm,1.524mm | 3.48 ± 0.05 | |
RT5870 | 0.127mm,0.787mm,0.254mm,1.575mm,0.381mm,3.175mm,0.508mm | 2.33 | |
RT5880 | 0.127mm,0.787mm,0.254mm,1.575mm,0.381mm,3.175mm,0.508mm | 2.20 | |
RO3003 | 0.13mm,0.25mm,0.50mm,0.75mm,1.52mm | 3.00 ±0.04 | |
RO3010 | 0.13mm,0.25mm,0.64mm,1.28mm | 10.2 ± 0.30 | |
RO3006 | 0.13mm,0.25mm,0.64mm,1.28mm | 6.15 ± 0.15 | |
RO3203 | 0.25mm,0.50mm,0.75mm,1.52mm | 3.02±0.04 | |
RO3210 | 0.64mm,1.28mm | 10.2±0.50 | |
RO3206 | 0.64mm,1.28mm | 6.15±0.15 | |
R03035 | 0.13mm,0.25mm,0.50mm,0.75mm,1.52mm | 3.50 ± 0.05 | |
RT6002 | 0.127mm,0.254mm,0.508mm,0.762mm,1.524mm,3.048mm | 2.94 ± 0.04 | |
RT6006 | 0.127mm,0.254mm,0.635mm,1.27mm,1.90mm,2.50mm | 6.15± 0.15 | |
RT6010 | 0.127mm,0.254mm,0.635mm,1.27mm,1.90mm,2.50mm | 10.2 ± 0.25 | |
TACONIC | TLX-8.TLX-9 | 0.508. 0.762 | 2.45-2.65 |
TLC-32 | 0.254,0.508,0.762 | 3.35 | |
TLY-5 | 0.254,0.508.0.8, | 2.2 | |
RF-60A | 0.254.0.508.0.762 | 6.15 | |
CER-10 | 0.254.0.508.0.762 | 10 | |
RF-30 | 0.254.0.508.0.762 | 3 | |
TLA-35 | 0.8 | 3.2 | |
ARLON | AD255C06099C | 1.5 | 2.55 |
MCG0300CG | 0.8 | 3.7 | |
AD0300C | 0.8 | 3 | |
AD255C03099C | 0.8 | 2.55 | |
AD255C04099C | 1 | 2.55 | |
DLC220 | 1 | 2.2 |